Capacitancia Variable
Capacitancia es la habilidad de una sustancia para mantener una carga eléctrica.
Un capacitor es un dispositivo que consiste en dos placas conductivas alineadas una con respecto a la otra pero sin hacer contacto. El espacio entre las placas
En electricidad y electrónica, un condensador o capacitor es un dispositivo formado por dos conductores o armaduras, generalmente en forma de placas o láminas separados por un material dieléctrico (siendo este utilizado en un condensador para disminuir el campo eléctrico, ya que actúa como aislante) o por el vacío, que, sometidos a una diferencia de potencial (d.d.p.) adquieren una determinada carga eléctrica.
A esta propiedad de almacenamiento de carga se le denomina capacidad o capacitancia. En el Sistema internacional de unidades se mide en Faradios (F), siendo 1 faradio la capacidad de un condensador en el que, sometidas sus armaduras a una d.d.p. de 1 voltio, estas adquieren una carga eléctrica de 1 culombio.
La capacidad de 1 faradio es mucho más grande que la de la mayoría de los condensadores, por lo que en la práctica se suele indicar la capacidad en micro- µF = 10-6, nano- F = 10-9 o pico- F = 10-12 -faradios. Los condensadores obtenidos a partir de súper condensadores (EDLC) son la excepción. Están hechos de carbón activado para conseguir una gran área relativa y tienen una separación molecular entre las "placas". Así se consiguen capacidades del orden de cientos o miles de faradios. Uno de estos condensadores se incorpora en el reloj Kinetic de Seiko, con una capacidad de 1/3 de Faradio, haciendo innecesaria la pila. También se está utilizando en los prototipos de automóviles eléctricos.
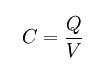
C: Capacidad
Q: Carga eléctrica
V: Diferencia de potencial
Principio de Operación del Sensor
Durante la operación del sensor el diafragma y el fluido de llenado en ambas cámaras del transmisor conducen la presión de proceso y la presión de referencia a los platos capacitivos que conforman el sensor.
La presión ejercida sobre los diafragmas es la que se ve reflejada como un cambio en la capacitancia del sensor. Los diafragmas se deforman en relación a la presión diferencial ejercida en ellos y esto a su vez genera un cambio en la señal que emiten las placas capacitivas. En el caso de la presión manométrica La cámara de baja del sensor de presión diferencial es colocada a la atmósfera. En el caso de los transmisores de Absoluta una presión de referencia es mantenida en la cámara de baja.
El sensor que se muestra utiliza la técnica de capacidad de dos conductores. La presión del proceso es transmitida, a través de diafragmas separadores y aceite siliconado, al diafragma sensible en el centro de la celda.
Los transmisores digitales de presión están diseñados para brindar diagnósticos avanzados y mejorar la precisión al utilizar buses de campo como salida estándar.
TIPOS
Los tipos de sensores de presión digitales básicamente se diferencian por su aplicación en cuanto al tipo de presión a medir. La parte constructiva de sus membranas son diseñadas y calculadas para captar el tipo de presión deseada, el procesamiento de la señal del sensor es muy parecida entre todos los tipos hasta llegar a su procesamiento de manera digital.
Por ello los principales tipos tenemos:
Sensor digital de presión Absoluta
Sensor digital de presión Diferencial
Sensor digital de presión relativa
Sensor digital de presión vacío
CONSTRUCCION
En la figura 2 se puede ver los componentes que conforman un sensor inteligente de presión.
Figura 2. Construcción de sensor digital de presión.
a) Salida Multibus: El sensor tiene la capacidad de dar una salida directamente en los terminales del sensor, debido a que el microprocesador esta incluido internamente en la carcaza del modulo sensor, esta salida puede ser 4-20 mA + Hart, Profibus, Foundation Fieldbus y Capacidades de Diagnostico Avanzado.
b) Carcaza Hermética de Acero Inoxidable: La carcaza del sensor es una sola pieza metálica maquinada completa y la cual permite aislar la humedad y evita la exposición del sensor y los componentes electrónicos al medio ambiente.
c) Doble Plato Capacitivo: Este es un nuevo diseño el cual presenta dos platos capacitivos como se muestra en la figura 3
Figura 3. Doble plato capacitivo.
Se usa para tener un mayor diagnostico en el sensor puesto que uno de los anillos es el que se utiliza para la medición y otro como referencia. Estos dos sensores se están comparando continuamente y cuando hay una diferencia entre los dos indica que el plato de medición esta dañado y envía una señal de alerta.
a) Diseño Coplanar: Es un diseño mejorado el cual permite tener las dos cámara en el mismo plano y elimina los errores de vibración o ruido que podrían afectar la medición, ya que es sensado por las dos cámaras por igual y es anulado.
b) Tecnología basada en microcontrolador: el transmisor inteligente trae internamente un microcontrolador que le permite ejecutar todas las rutinas de medición y de diagnósticos avanzados. Como por ejemplo como se muestra en la siguiente figura el transmisor esta en la capacidad de aprender del proceso y generar una alarma cuando comienza a detectar obstrucciones en sus líneas de impulso.
Figura 4. Transmisor inteligente.
CIRCUITO DE ACONDICIONAMIENTO DE SEÑAL
La figura 5 muestra el diagrama en bloques básico de un sensor digital de presión capacitivo. la cual está constituida de cuatro bloques que son el sensor, el cual se encarga de obtener una diferencia de capacitancias mediante el capacitor que varía con la presión y un capacitor de referencia; conversión de capacitancia a voltaje, una vez obtenida esa capacitancia se convierte a voltaje mediante un integrador; conversión analógica a digital, se obtiene una palabra binaria que representa al voltaje obtenido de la diferencia de capacitancias; bloque de codificación o display, a la palabra binaria obtenida se le asigna una valor que representa la diferencia de capacitancia obtenida, la cual es mostrada en un display.

Figura 5. Diagrama en bloques básico de un sensor digital de presión capacitivo
El sensor de presión capacitiva detecta la presión aplicada por medio de la flexión del diafragma. Para una simple estructura, la flexión del diafragma es proporcional a la presión P aplicada. Por lo que la capacitancia del sensor C(P) cambia hiperbólicamente y es aproximada por
C(P) = Co + DC(P) (1)
esta variación de capacitancia esta representada por medio un tangente hiperbólica, la expresión final está es función de la flexión (W) que sufre el sensor en lugar de la presión, por lo que la relación de la ecuación 1 queda definida como
C(W) = Co + DC(W) (2)
donde C(W) es el valor de la capacitancia debido a la flexión del sensor, donde Co es la capacitancia del sensor cuando la presión es cero, a la cual se le puede conocer como la variación de capacitancia.
Enfocandonos principalmente en los circuitos que conforman las etapas de procesamiento de señal tenemos:
Conversión Capacitancia-voltaje
La operación del circuito se divide en 2 fases o estados. En el estado de reinicio, en el cual el
circuito inicializa o descarga todos los capacitares. (Figura 6a). El siguiente estado (Figura 6b) se conoce como sensado, este toma la capacitancia diferencial DC entre CX y Cr, para producir el voltaje Vo proporcional a DC.

Figura 6. Circuito Convertidor Capacitancia-Voltaje.
siendo
El op amp debe cumplir con ciertos requisitos para satisfacer nuestras necesidades. Ya que la ganancia de voltaje no puede ser infinita debe ser muy grande para que en la ecuación sea despreciable, también debe cumplir con las siguientes especificaciones: el voltaje de desviación (offset) de entrada debe ser muy pequeño, tener una la corriente inversa de entrada baja, una alta impedancia a la entrada, velocidad de respuesta alta, compensación interna.
Conversión Analógico-digital
Una vez obtenido el voltaje que representa la variación de la capacitancia se convierte a señal digital. A nivel de diseño, en este caso se piensa utilizar un dispositivo de conversión conocido como ADC, en el cual deben considerarse la tiempo de conversión, la ganancia, su linealidad, sensibilidad de la fuente de conversión, principios de ajuste a ganancia cero, rangos de alimentación, precisión y los coeficientes de temperatura.
Un circuito integrado con mucha prestación para esta necesidad en el ICL7107. Su selección se debe principalmente a que su salida es de tres dígitos y medio, lo cual quiere decir que internamente tiene un decodificador de siete segmentos, el cual entrega tres dígitos del 0-9 y el medio dígito, que es el más significativo, es de 0-1. Esto quiere decir que realiza cuentas de 0 hasta ±1999, lo cual corresponde aproximadamente a un convertidor de 11 bits (2,047 pasos). El dispositivo tiene una potencia de disipación de 10mW, una corriente de entrada de 1pA, bajos niveles de ruido de 15mVp-p, garantiza lecturas de cero para entradas a cero voltios, se alimenta con voltajes máximos de 6V en V+ y –9V en V-.
El rango de temperatura de trabajo es de 0º C hasta 70º C. Tiene una diferencia de error de ±1 entre paso y paso, una razón de rechazo a modo común de 50 mV/V. Comúnmente el ADC tiene una frecuencia de conversión por 48 kHz, pero su rango de conversión esta en 240 kHz, 120 kHz, 80 kHz, 60 kHz, 48 kHz, 40 kHz, y 331/3 kHz .
En el esquemático de la Fig. 7 se muestra la configuración del ADC con su etapa de acondicionamiento de la señal.
Figura 7. Esquemático del convertidor A/D con su acondicionamiento de señal.
En donde con la siguiente ecuación dimensionamos el voltaje de referencia a partir de la cuenta max deseada.
En este bloque se hace la relación entre la palabra binaria obtenida y presión aplicada al sensor,
con la finalidad de mostrarla en un display en unidades de psi u otra.
APLICACIÓN INDUSTRIAL
Los sensores de presión digital tienen como principales aplicaciones la medición de tres variables Presión, Flujo y Nivel
En el ámbito industrial podemos mencionar entre sus posibles aplicaciones en áreas de:
- Gas y Petróleo
- Alimentación, bebidas y farmacéutica.
- Química
- Generación de energía
- Siderurgia
- Aviación
- Militar
- Pulpa y papel
- Entre muchas otras.
EJEMPLO DE APLICACIÓN INDUSTRIAL REAL
Aplicación
Control y medición de consumo de Oxigeno para una planta Acerera.
Descripción
El objetivo de esta aplicación es monitorear y controlar la cantidad de oxigeno suministrado por cada una de las líneas a los hornos a través del uso de medidores de presión diferencial generada por placas orificios colocadas en cada línea de inyección de oxigeno.
La suma total del oxigeno suministrado por las líneas es monitoreado y contabilizado a través de un DCS (Sistema de control distribuido) al cual llegan las señales digitales de cada Trasmisor de presión diferencial inteligente.

Figura 8. Transmisores de presión diferencial inteleigente instalados.
Figura 9. Transmisor de presión diferencial inteligente instalado en la aplicacion.
PROBLEMA PRACTICO
En una planta de manejo de resinas se desea medir el nivel de un tanque de almacenamiento de Agua.
Para esta aplicación conocemos los datos del tanque:
Altura: 18 mts y es un Tanque Abierto

Presión hidrostática
Un fluido pesa y ejerce presión sobre las paredes, sobre el fondo del recipiente que lo contiene y sobre la superficie de cualquier objeto sumergido en él. Esta presión, llamada presión hidrostática provoca, en fluidos en reposo, una fuerza perpendicular a las paredes del recipiente o a la superficie del objeto sumergido sin importar la orientación que adopten las caras.
Basados en el concepto de presión hidrostática y conociendo la altura del tanque podemos determinar el margen de medida del instrumento tomando en cuenta que la presión hidrostática es igual:
P= ρ.g.h
De donde la altura es relación directa de la presión que ejerce la columna de agua. Tomando en cuenta que 10 m de columna de agua equivalen a 1 barg o 14.7 psig.
Entonces en nuestro caso como el tanque es de 18 m (26.46 Psig) debemos seleccionar un medidor con un margen de medida 0 a 50 psig. Y seleccionamos el instrumento con salida digital en protocolo Foundation Fieldbus para hacer uso de los diagnósticos avanzados y tener la posibilidad de ejercer el control en el campo.
5 comentarios:
Muy Buena la página... La voy a usar para un informe de Medidas Electricas.. :D
Gracias muuuy buen articulo
Gracias muuuy buen articulo
Muy buena informacion sobre las Celdas de Carga, desconocia alguna de ellas.
Muchas gracias, me ayudo mucho.
Publicar un comentario